Inovus Making Innovation - Med-tech
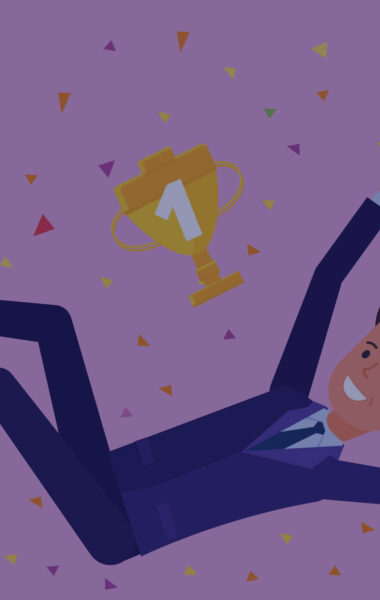
Posted by Helen Hanson. 3rd November 2019
Inovus Medical features in the latest issue of Med Tech Innovation News
“Ian Bolland talks to Dr Elliot Street, CEO and Co-founder of Inovus Medical the company is brimming with medtech solutions including products that let training surgeons practice away from patients on material that behaves like real tissue”
Inovus Medical has come a long way since the development of its first laparoscopic box trainer and the formation of the company in 2012.The company is expanding rapidly, with the majority of its manufacturing – including 3D printing – now being carried out in its factory based in St Helens. While the team build its surgical simulation devices which are specifically designed to support trainee surgeons in mastering their surgical techniques, it also develops its own electronics and consumable products with a level of functionality and realism it feels is unmatched by its competitors worldwide. The design team continues to develop innovative ways of enhancing the portfolio of products.
This year alone has seen £1 million investment going towards design of a new laparoscopic AR system which is to be launched early 2020.Dr Elliot Street, who worked as a junior doctor in the early years of the business is the CEO and co-founder, explains that after the initial formation of the company and those first few challenging years the company is now at the stage where it is expanding in key business areas, and investing in equipment and processes that will see Inovus Medical go from strength to strength.
He said: “What we wanted to do first was answer an unmet need in the world of surgical training and specifically laparoscopic training, so we set up a company with three strong core values that major on accessibility, affordability and functionality. “Initially the key focus was to develop extremely affordable box trainers that trainee surgeons could benefit from using, at a price they could afford.
When we started it was just a webcam in a plastic box. I was a medical student and Jordan (Van Flute), co-founder and CTO, had just graduated. We saw a gap in terms of what was being delivered in training and there was a real lack of access to good quality, affordable laparoscopic trainers. “The first product we made, we bent a piece of plastic with a heat gun around the side of a fridge and drilled some holes in it. We produced a couple of promotional shots, coded our own website, uploaded it online and sold our first laparoscopic box trainer. We used the money to purchase a more efficient device for shaping the plastic, from that point every time we sold a box trainer, we upgraded our machinery.”
Along with the box trainers that one may be more accustomed to, the company also manufactures in house, a range of consumables which have been designed and developed using materials that act in the same way as real tissue. This allows realistic models to be placed inside the box trainers and operated on.
Thanks to the recent investment the company is bringing these medical models to life through the use of Augmented Reality. Dr Street explained that a major driver of the idea was to provide the trainees the ability to perform a virtual procedure in the most realistic way – repeatedly stating his desire for products to be affordable, accessible and functional. The simulators that are being developed include those that can be taken home, as well as those that can be used in an institutional setting.
“Our haptics are real haptics. You don’t need sensors because we’re putting in models that feel and act with a level of realism unexperienced to date. The thing that’s giving you all that haptic feedback is a real, tangible model and then we build a digital environment around that to increase the level of realism and immersion.
“You can’t beat the haptics of using the instruments you’re going to use in real life and picking up materials that replicate real tissue and even give the same tension you would expect of real tissue. Some materials we have are proprietary to us and we have invested a great deal of time developing them to fulfil our customer’s requirements, these newly developed materials allow the use of energy devices in a simulated environment as they react in much the same way as real tissue when subject to these devices.”
“We’re taking the empathetic insight of what our customers are going through and the difficulty they have with delivering or taking part in surgical simulation training and we’re saying: ‘leave that with us, we’ll find the answer.’
“Thanks to the Inovus products training surgeons are now able to practice in a safe, controlled environment away from the patients but on a material, that is behaving like a real tissue behaves.”
It’s not just surgeons who can be the beneficiaries, as medical device companies can also show their products in the best light with a more realistic tissue while displaying them to potential customers. “We’re offering them a product that shows their instruments in the best light so when they want to go and demo to a customer, they’re able to use non-animal by-products so they don’t contaminate their demo kit.”
During the last three months the company’s product range have been showcased and received with great interest and excitement at some of the most acclaimed global congress’ held across the globe”.
With an increase in interest from customers both clinical and business led and the added advantage of some substantial funding from investors and innovation awards Inovus has now grown to a team of 18 strong with expertise in, manufacturing, engineering, electronics, design, software, import & export (across the globe) and marketing.
As demand for Inovus Medical products has increased significantly during the start of 2019 with two of the existing products relying heavily on 3D printing and with a further three new products under development that will require printed parts.
The company has invested in a production level SLS 3D printer, supplied by 3D Systems, allowing them to manufacture their plastic parts with a finish level equivalent to that of injection moulding.
Speaking about its relationship with Inovus, Simon van de Crommert, sales manager of 3D Systems in the UK, Ireland and Benelux, said: “I first met Inovus at an exhibition in the UK. Inovus visited our stand as they were struggling with the high tooling cost and long lead times associated with their new products. Inovus is a small, innovative medical company in need of a new cost-effective, low-volume production method for their new products to help reduce the product development cycle and accelerate time to market.”
Inovus’ plans for the months ahead will see the launch of a range of products that will have technological advanced features as the company moves towards the introduction of augmented reality simulation devices – aimed to further enhance the surgical trainees experience.
To download the full article go to:
https://www.med-technews.com/med-tech-innovation-news-issue-45-november-december-2019/