Inovus Medical incoprorates additive manufacturing
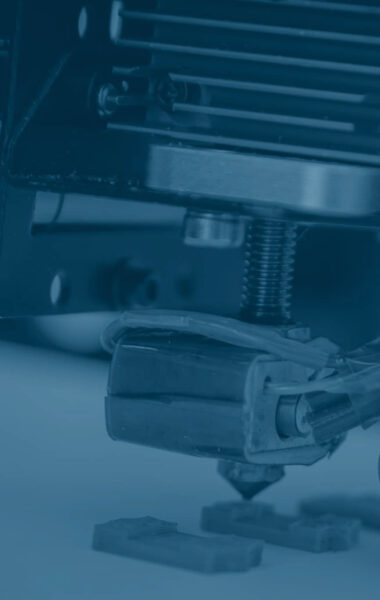
Posted by Helen Hanson. 24th May 2019
Inovus Medical adds production level 3D printing to their manufacturing armamentarium
Inovus Medical has this week announced the installation of the world’s most advanced 3D printing technology to its manufacturing facility in St Helens, Merseyside.
The production level SLS 3D printer, supplied by 3D Systems, allows the company to produce plastic parts with a finish level equivalent to that of injection moulding but without the expensive up front cost of tooling and manufacturing of injection moulds. The printer uses selective laser sintering, a form of 3D printing that negates the need for adding support structures in the printing process, vastly increasing printer bed utilisation and production capacity. Two of Inovus’ existing products, the Bozzini® Hysteroscopy simulator and Sellick the cricoid pressure trainer, rely heavily on 3D printing and with a further three new products under development that will require printed parts, the addition of the technology will ensure Inovus are able to adequately scale their manufacturing capabilities as demand for their products continues to grow.
The use of the SLS technology for manufacturing large scale commercially viable products is not something often seen with 3D printing, a technology that is widely used for rapid prototyping and small scale projects but has found it difficult to translate into the wider manufacturing sector. Inovus has however, taken a contrarian approach to deployment of the technology allowing the company to use SLS printing as a main stay in its manufacturing processes; an approach that caught the attention of printer supplier 3D systems.
Having heard of the novel approach Inovus use to maximize efficiencies in the printer, 3D systems featured the company in one of their case studies.
Inovus CTO, Jordan Van Flute said: “The addition of production level 3D printing to our manufacturing armamentarium is an exciting step forward as we continue to drive vertical integration within the company. Its particularly pleasing to know we are using additive manufacturing to actually manufacture commercially available products, something that we feel is a real paradigm shift for the 3D printing sector, feelings that are clearly shared by our suppliers 3D Systems.
It has been a steep learning curve bringing SLS printing and all the requisite post processing activity in house but we are now seeing the benefits that this approach has had in assisting us to drive our business forward.”